Moulage en coquilleest un processus dans lequel le sable mélangé à une résine thermodurcissable peut entrer en contact avec une plaque à motif métallique chauffée, de sorte qu'une coque de moule fine et solide se forme autour du motif. Ensuite, la coque est retirée du modèle et la chape et la traînée sont retirées ensemble et conservées dans un flacon avec le matériau de secours nécessaire et le métal en fusion est versé dans le moule.
Généralement, pour préparer le sable de moulage en coquille, on utilise du sable sec et fin (90 à 140 GFN), totalement exempt d'argile. La granulométrie à choisir dépend de l'état de surface souhaité sur la pièce moulée. Une granulométrie trop fine nécessite une grande quantité de résine, ce qui rend le moule coûteux.
Les résines synthétiques utilisées dans le moulage en coque sont essentiellement des résines thermodurcissables, qui durcissent de manière irréversible par la chaleur. Les résines les plus utilisées sont les résines phénol-formaldéhyde. Associés au sable, ils présentent une très grande solidité et résistance à la chaleur. Les résines phénoliques utilisées dans le moulage en coque sont généralement du type à deux étapes, c'est-à-dire que la résine contient un excès de phénol et agit comme un matériau thermoplastique. Lors de l'enrobage avec le sable, la résine est combinée à un catalyseur tel que l'hexaméthylène tétramine (hexa) dans une proportion d'environ 14 à 16 % de manière à développer les caractéristiques thermodurcissables. La température de durcissement de ceux-ci serait d'environ 150 °C et le temps nécessaire serait de 50 à 60 secondes.
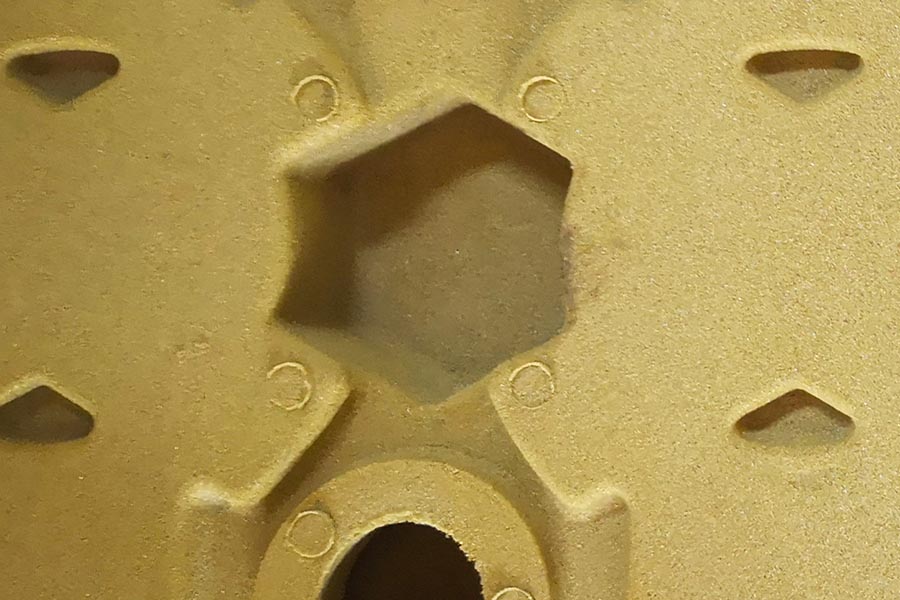
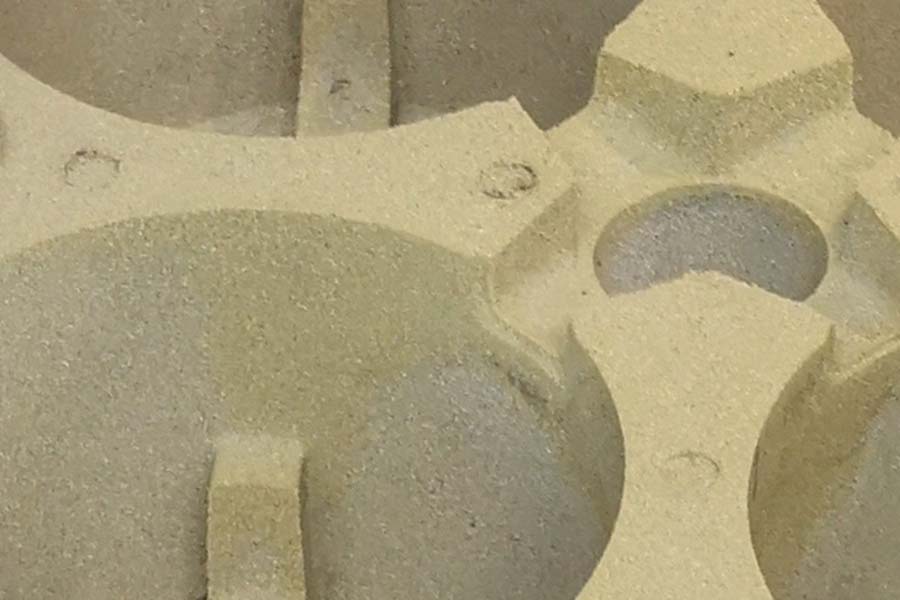
Avantages du processus de moulage en coquille
1.Pièces moulées en coquillesont généralement plus précis dimensionnellement que les moulages en sable. Il est possible d'obtenir une tolérance de +0,25 mm pour les pièces moulées en acier et de +0. 35 mm pour les fontes grises etpièces moulées en fonte ductiledans des conditions normales de travail. Dans le cas de moules carapaces à tolérances serrées, on peut l'obtenir dans la plage de +0,03 à +0,13 mm pour des applications spécifiques.
2. Une surface plus lisse peut être obtenue dans les pièces moulées en coquille. Ceci est principalement obtenu grâce aux grains plus fins utilisés. La plage typique de rugosité est de l'ordre de 3 à 6 microns.
3. Les angles de dépouille, qui sont inférieurs aux moulages en sable, sont nécessaires dans les moules en coquille. La réduction des angles de dépouille peut aller de 50 à 75%, ce qui permet d'économiser considérablement les coûts de matériaux et les coûts d'usinage ultérieurs.
4. Parfois, des noyaux spéciaux peuvent être éliminés lors du moulage en coque. Étant donné que le sable a une résistance élevée, le moule pourrait être conçu de telle manière que les cavités internes puissent être formées directement en nécessitant des noyaux de coque.
5. De plus, des sections très fines (jusqu'à 0,25 mm) du type de culasses refroidies par air peuvent être facilement réalisées par moulage en coque en raison de la résistance plus élevée du sable utilisé pour le moulage.
6. La perméabilité de la coque est élevée et aucune inclusion de gaz ne se produit donc.
7. Une très petite quantité de sable doit être utilisée.
8. La mécanisation est facilement possible en raison de la simplicité du traitement impliqué dans le moulage en coque.
Limites du processus de moulage en coquille
1. Les modèles sont très chers et ne sont donc économiques que s'ils sont utilisés dans une production à grande échelle. Dans une application typique, le moulage en coque devient plus économique que le moulage en sable si la production requise est supérieure à 15 000 pièces en raison du coût plus élevé du modèle.
2. La taille de la pièce moulée obtenue par moulage en coque est limitée. Généralement, des pièces moulées pesant jusqu'à 200 kg peuvent être fabriquées, bien qu'en plus petite quantité, des pièces moulées pesant jusqu'à 450 kg soient fabriquées.
3. Il n’est pas possible d’obtenir des formes très compliquées.
4. Un équipement plus sophistiqué est nécessaire pour manipuler les coques moulées, comme ceux requis pour les modèles métalliques chauffés.
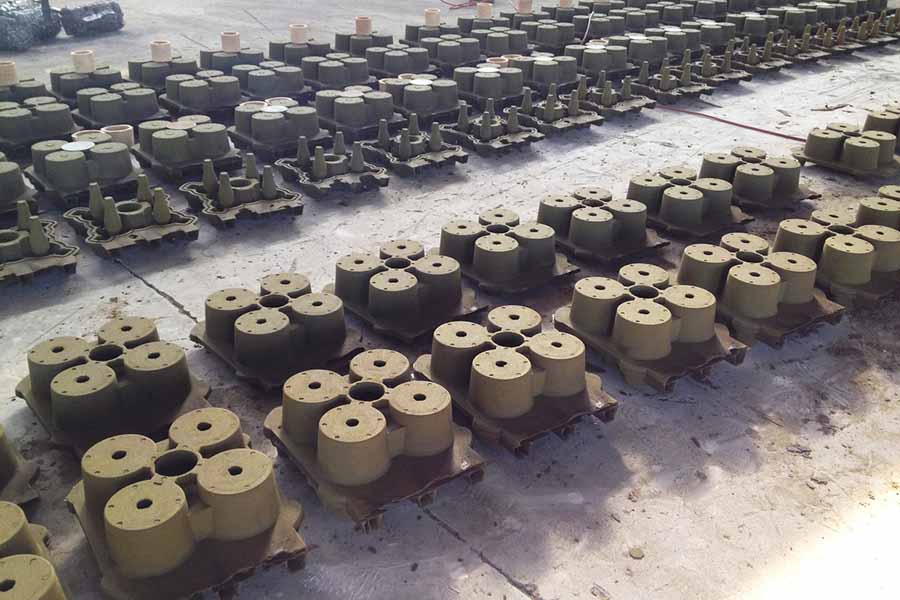
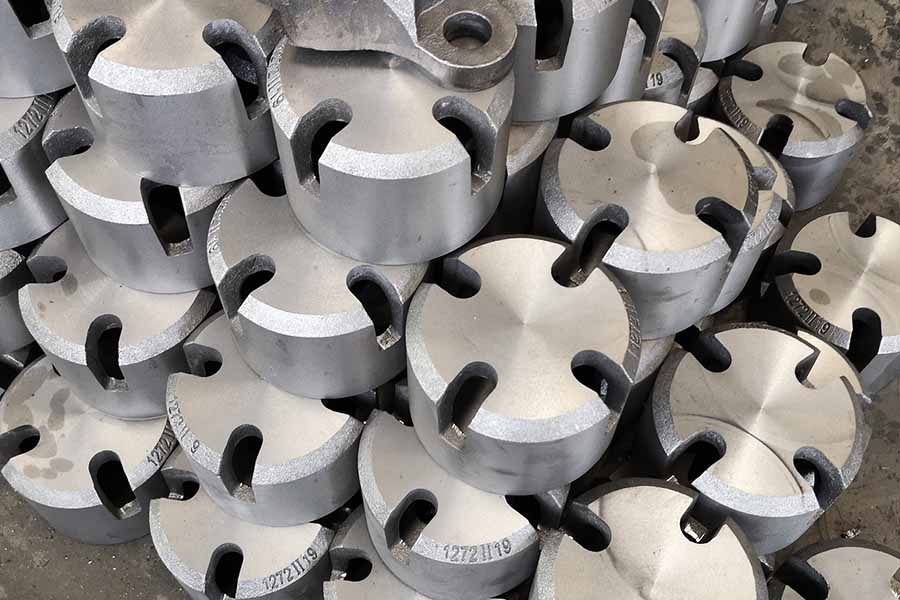
Heure de publication : 25 décembre 2020