Le moulage à modèle perdu consiste à recouvrir plusieurs couches de revêtements réfractaires sur la surface du moule en cire.Après durcissement et séchage, le moule en cire est fondu par chauffage pour obtenir une coque avec une cavité correspondant à la forme du moule en cire.Après cuisson, il est coulé dans Une méthode d'obtention de moulages, on l'appelle aussi moulage à la cire perdue.Avec l'amélioration continue de la technologie de production, de nouveaux procédés de moulage à la cire continuent d'apparaître et la variété des matériaux disponibles pour le moulage augmente.Désormais, la méthode de démoulage n'est plus limitée à la fusion et les matériaux de moulage ne sont plus limités aux matériaux en cire.Des moules en plastique peuvent également être utilisés.Étant donné que les pièces moulées obtenues par cette méthode ont une précision dimensionnelle plus élevée et des valeurs de rugosité de surface inférieures, on parle également de coulée de précision.
La caractéristique de base demoulage de précisionest qu'un moule jetable fusible est utilisé lors de la fabrication de la coque.Puisqu'il n'est pas nécessaire de dessiner le moule, la coque est intégrale sans surface de séparation, et la coque est constituée de matériaux réfractaires avec d'excellentes performances à haute température.Le moulage à modèle perdu peut produire des pièces moulées de forme complexe, avec une épaisseur de paroi minimale de 0,3 mm et un diamètre minimal du trou de coulée de 0,5 mm.Parfois en production, certaines pièces composées de plusieurs pièces peuvent être combinées en un tout en modifiant la structure et directement formées par moulage à la cire perdue.Cela peut économiser des heures de travail et la consommation de matériaux métalliques, et rendre la structure dupièces couléesplus raisonnable.
Le poids des pièces moulées produites par moulage à la cire perdue varie généralement de quelques dizaines de grammes à plusieurs kilogrammes, voire des dizaines de kilogrammes.Les pièces moulées trop lourdes ne conviennent pas au moulage de précision en raison de la limitation des performances du matériau de moulage et de la difficulté à fabriquer la coque.
Pièces moulées produites par moulage à la cire perduene sont pas limités par les types d'alliages, en particulier pour les alliages difficiles à couper ou à forger, ce qui peut montrer sa supériorité.Cependant, la production de moulage de précision présente également certaines lacunes, principalement en raison du grand nombre de processus, des longs cycles de production, des processus technologiques complexes et de nombreux facteurs affectant la qualité des pièces moulées, qui doivent être strictement contrôlées pour stabiliser la production.
Par rapport à d'autres méthodes de coulée, la caractéristique remarquable de la coulée à la cire perdue est l'utilisation de moules fusibles pour fabriquer la coque.Un moule de revêtement est consommé à chaque fois qu'une coque est fabriquée.La condition préalable nécessaire pour obtenir des pièces moulées de haute qualité avec une précision dimensionnelle élevée et de faibles valeurs de rugosité de surface est un moule de revêtement avec une précision dimensionnelle élevée et de faibles valeurs de rugosité de surface.Par conséquent, les performances du matériau de moulage (appelé matériau de moulage), la qualité du moulage (le modèle utilisé pour presser le revêtement) et le processus de moulage affecteront directement la qualité du moulage de précision.
Les moules de fonderie de précision sont actuellement généralement utilisés dans une coque en matériaux réfractaires multicouches.Une fois le module trempé et recouvert d'un revêtement réfractaire, saupoudrez le matériau réfractaire granulaire, puis séchez et durcissez, et répétez ce processus plusieurs fois jusqu'à ce que la couche de matériau réfractaire atteigne l'épaisseur requise.De cette manière, une coque multicouche est formée sur le module, qui est généralement garé pendant une période de temps pour sécher et durcir complètement, puis démoulé pour obtenir une coque multicouche.Certaines coques multicouches doivent être remplies de sable, d'autres non.Après la torréfaction, ils peuvent être versés directement, ce qui s'appelle une coque à haute résistance.
La qualité de la coque est directement liée à la qualité de la coulée.Selon les conditions de travail de la coque, les exigences de performance de la coque comprennent principalement :
1) Il a une résistance à température normale élevée, une résistance à haute température appropriée et une faible résistance résiduelle.
2) Il a une bonne perméabilité à l'air (en particulier la perméabilité à l'air à haute température) et une bonne conductivité thermique.
3) Le coefficient de dilatation linéaire est faible, la dilatation thermique est faible et la dilatation est uniforme.
4) Excellente résistance au froid et à la chaleur rapides et stabilité thermochimique.
Ces propriétés de la coque sont étroitement liées aux matériaux utilisés dans la fabrication de la coque et au processus de fabrication de la coque.Les matériaux de coque comprennent les matériaux réfractaires, les liants, les solvants, les durcisseurs, les tensioactifs, etc. Parmi eux, le matériau réfractaire et le liant forment directement la coque, qui est le matériau principal de la coque.Les matériaux réfractaires utilisés dans la fonderie de précision sont principalement des réfractaires de sable de silice, de corindon et d'aluminosilicate (tels que l'argile réfractaire et l'aluminium banadium, etc.).De plus, du sable de zircon et du sable de magnésie sont parfois utilisés.
Le matériau réfractaire en poudre et le liant sont préparés en revêtement réfractaire, et le matériau réfractaire granulaire est saupoudré sur le revêtement réfractaire lors de la fabrication de la coque.Les liants utilisés dans les revêtements réfractaires comprennent principalement l'hydrolysat de silicate d'éthyle, le verre soluble et le sol de silice.La peinture préparée avec du silicate d'éthyle présente de bonnes propriétés de revêtement, une résistance élevée de la coque, une faible déformation thermique, une précision dimensionnelle élevée des pièces moulées obtenues et une bonne qualité de surface.Il est principalement utilisé pour produire d'importantes pièces moulées en acier allié et d'autres pièces moulées avec des exigences de qualité de surface élevées.La teneur en SiO2 du silicate d'éthyle produit en Chine est généralement de 30% à 34% (fraction massique), on l'appelle donc silicate d'éthyle 32 (32 représente la fraction massique moyenne de SiO2 dans le silicate d'éthyle).Le silicate d'éthyle ne peut jouer un rôle de liaison qu'après hydrolyse.
La coque de revêtement préparée avec du verre soluble est facile à déformer et à se fissurer.Par rapport au silicate d'éthyle, les pièces moulées produites ont une faible précision dimensionnelle et une rugosité de surface élevée.Le liant de verre soluble convient à la production de petites pièces moulées en acier ordinaires etmoulages en alliage non ferreux.Le verre soluble pour la coulée de précision a généralement un module de 3,0 ~ 3,4 et une densité de 1,27 ~ 1,34 g/cm3.
Le liant de sol de silice est une solution aqueuse d'acide silicique, également connu sous le nom de sol de silice.Son prix est 1/3 ~ 1/2 inférieur à celui du silicate d'éthyle.La qualité des moulages produits en utilisant le sol de silice comme liant est supérieure à celle du verre soluble.Le liant a été grandement amélioré.Le sol de silice a une bonne stabilité et peut être stocké pendant une longue période.Il ne nécessite pas de durcisseurs spéciaux lors de la fabrication de coques.La résistance à haute température de la coquille est meilleure que celle des coquilles de silicate d'éthyle, mais le sol de silice a une mauvaise mouillabilité par rapport au revêtement et prend plus de temps à durcir.Les principaux processus de fabrication de coques comprennent le dégraissage des modules, le revêtement et le ponçage, le séchage et le durcissement, le démoulage et la torréfaction.
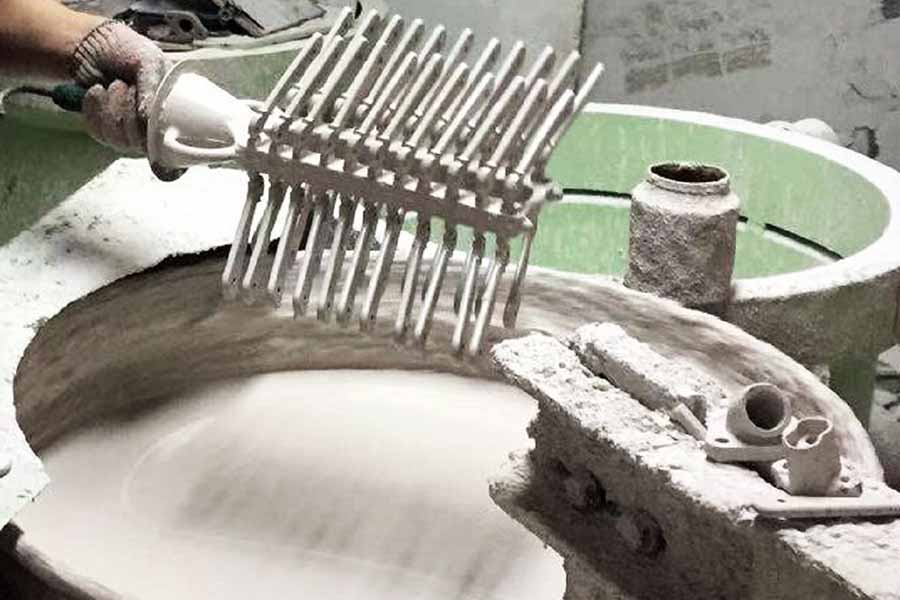
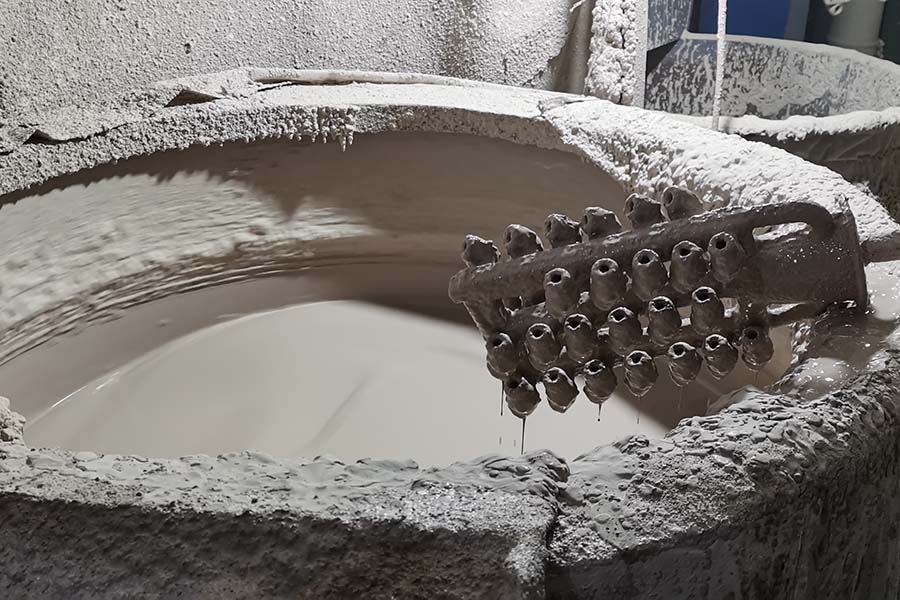
Heure de publication : 11 février 2021