Comme nous le savons tous, le moulage de précision produit lemoulagesavec précision et bonne finition. Cependant, au cours du processus de production demoulage de précision, il existe de nombreux défauts de coulée courants possibles. Sur la base de notre expérience en ingénierie et de nos équipements de pointe, nous pouvons trouver un moyen de prévenir de tels problèmes en analysant les causes. Ci-dessous, nous présentons plusieurs défauts de coulée courants ainsi que leurs causes et méthodes de prévention. J'espère que cet article sera utile à nos clients pour comprendre les problèmes et à nos collègues, cette analyse pourrait vous aider à prévenir d'éventuels défauts de coulée.
Sous-couche et barrière contre le froid
1. Description du problème :
Le sous-casting manque souvent de viande localement dans la fine paroi du moulage ou à l'écart du canal intérieur, et son bord est en forme d'arc. La cloison froide est que deux brins de métal en fusion ne sont pas complètement fusionnés et qu'il y a des joints évidents.
2. Cause :
1) Faible température de coulée du métal fondu et température du moule
2) La vitesse de coulée est lente ou le réglage du canal est déraisonnable, le flux de métal est trop long
3) L'épaisseur de la paroi de la pièce moulée est trop fine et l'écoulement du métal en fusion est médiocre
4) Coupé pendant le versement
3. Mesures préventives :
1) Augmenter la température de coulée du métal fondu et la température du moule
2) Augmentez la vitesse de coulée ou augmentez le nombre ou la surface du canal intérieur pour réduire le flux de métal en fusion
3) Augmentez la hauteur de pression de la colonne montante pour éviter toute coupure pendant le versement.
Rétrécissement
1. Description du problème :
On ne peut le trouver que par inspection aux rayons X. Le retrait de surface peut être détecté par fluorescence ou par coloration. Dans les cas graves, on peut le retrouver après un soufflage de sable.
2. Cause :
1) La structure de casting est déraisonnable et les points chauds sont trop nombreux ou trop grands
2) La capacité thermique de la colonne montante verseuse est faible, ce qui ne parvient pas à former une solidification séquentielle, ou la tête de pression est petite, ce qui réduit la capacité d'alimentation.
3) La température du moule est basse, la vitesse de refroidissement est rapide et le canal d'alimentation est bloqué
3. Mesures préventives :
1) Améliorer la structure de coulée et réduire les points chauds
2) Réglez la colonne montante de manière raisonnable, ou ajoutez une nervure d'alimentation qui peut être retirée par les méthodes de traitement, augmentez la tête de pression, de sorte que lemoulages de précisionpeut être solidifié séquentiellement sous l'action d'une certaine tête de pression
3) Augmentez de manière appropriée la température de coulée et la température du moule pour ralentir la vitesse de refroidissement.
Fissure chaude
1. Description du problème :
Des fissures intergranulaires irrégulières se produisent en surface ou à l'intérieur et la surface est oxydée. Il peut être observé après un nettoyage approfondi du sable, et seule une légère inspection de traitement ou de pénétration peut être trouvée.
2. Causes :
1) Cela est lié à la composition de l'alliage, la teneur en carbone et en silicium est élevée, la plage de température de la phase liquide-solide est large et la fissuration à chaud est facile
2) Faible température du moule, mauvaise aptitude au retrait et taux de refroidissement rapide
3) L'épaisseur de la pièce moulée varie considérablement et le congé de transition est trop petit
3. Mesures préventives :
1) Pour les alliages ou aciers sujets aux fissures à chaud, leur teneur en carbone et en silicium doit être contrôlée autant que possible jusqu'aux limites moyennes et inférieures.
2) Augmentez la température du moule pendant la coulée, ralentissez la vitesse de refroidissement de la pièce moulée ou réduisez la résistance de la coque du moule.
3) Ajouter des nervures de procédé anti-fissuration au niveau des joints de l'épaisseur des pièces moulées, ou augmenter les congés de transition
Fissure froide
Nom et caractéristiques :
Il y a des fissures pénétrantes continues sur la pièce moulée. Une surface brillante ou une surface légèrement oxydée apparaît au niveau de la fracture.
Causes
1. Pendant le processus de refroidissement de la pièce moulée, le retrait est empêché, ce qui entraîne des contraintes thermiques et des contraintes de changement de phase, et ces contraintes dépassent la résistance du matériau à l'état élastique et provoquent une rupture.
2. Lors du nettoyage de la coque, de la découpe de la porte, de la contremarche ou lors du réglage, la pièce moulée avec contrainte résiduelle est soumise à une force externe pour provoquer une rupture.
Méthodes de prévention
1. Ajoutez des nervures de renforcement au niveau des fissures froides pour améliorer la possibilité de retraitement de la forme, réduisant ainsi la résistance au retrait et les contraintes de coulée.
2. Lors du processus de post-coulée, évitez les chocs violents entre les coulées.
Évent
Nom et caractéristiques
Il y a des trous évidents ou discrets avec une surface intérieure lisse sur le moulage.
Causes
1. Mauvaise perméabilité à l'air de la coque du moule, ce qui fait qu'il est trop tard pour que le gaz présent dans la cavité soit évacué pendant le coulage.
2. Cuisson insuffisante de la forme de la coque, entraînant une élimination insuffisante des résidus de matériau de moulage et des matériaux produisant des gaz dans le matériau de la coque.
3. La teneur en gaz liquide métallique est trop élevée, ce qui entraîne une mauvaise désoxydation.
4. Le réglage du système de versement est déraisonnable, ce qui entraîne l'implication de gaz humains dans le versement.
Méthodes de prévention
1. Améliorez la perméabilité à l'air de la coque et ajoutez des aérations si nécessaire.
2. Obus entièrement tiré.
3. Améliorer les méthodes de désoxydation.
4. Améliorer le système de contrôle.
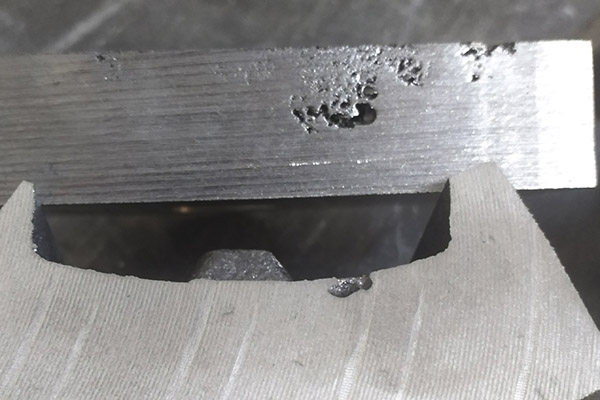
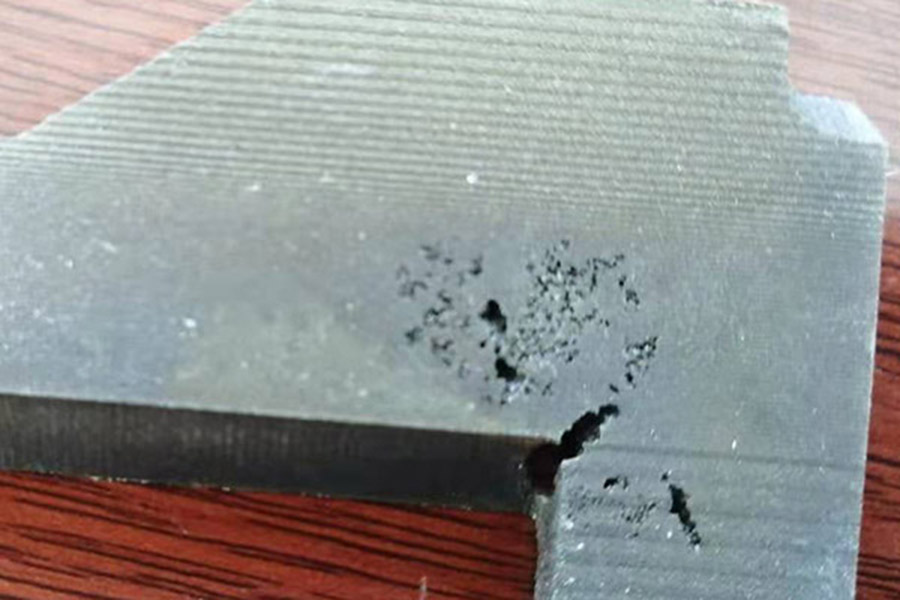
Piqûres de coulée
Nom et caractéristiques
Il y a des piqûres denses en forme de points sur la surface du moulage.
Causes
1. Lorsque le silicate d'éthyle est utilisé comme liant, l'hydrolysat incomplet est dans le processus de revêtement, l'humidité relative intérieure est trop faible, de sorte que l'hydrolysat ne peut pas être hydrolysé davantage et le « givre blanc » est précipité après la torréfaction.
2. Lorsque le verre soluble est utilisé comme liant, le sel résiduel dans la coque du moule réagit avec le métal fondu pour former une fosse.
3. Le métal en fusion est mal désoxydé ou les scories ne sont pas nettoyées lors du taraudage.
Méthodes de prévention :
1. Lorsque vous utilisez du silicate d'éthyle comme liant, augmentez de manière appropriée la quantité d'eau ajoutée et augmentez l'humidité relative de l'atelier de peinture pour minimiser les hydrolysats incomplets résiduels.
2. Lorsque vous utilisez du verre soluble comme liant, nettoyez la coque avec de l'eau acidifiée après décirage.
3. Remplacez le revêtement de surface par du sol de silice comme liant.
4. Pendant la fusion, renforcez la désoxydation et l'élimination des scories.
Moulage d'un sténopé sous-cutané
Nom et caractéristiques
Une fois la surface du moulage polie, de minuscules points noirs apparaissent. Ce phénomène se produit principalement dansacier inoxydable nickel-chromel.
Causes :
1. Trop de matériaux recyclés sont utilisés lors de la fusion du métal ou le matériau recyclé n'a pas été traité correctement.
2. Pendant le processus de fusion, le métal fondu est oxydé ou le métal fondu absorbe du gaz, ce qui entraîne une désoxydation insuffisante.
3. La teneur en impuretés du matériau de la coque est trop élevée ou l'agent de liaison et le métal fondu ont une réaction chimique.4. Réglage déraisonnable du système de contrôle.
Méthodes de prévention :
1. Contrôlez ou réduisez la quantité de matériaux recyclés, et les matériaux recyclés doivent être utilisés après le soufflage de sable ou le grenaillage.
2. Contrôlez strictement le processus de fusion et renforcez la désoxydation.
3. Utilisez du corindon fondu, du sable de zircon et du sol de silice ou de la peinture au silicate d'éthyle.
4. Essayez d'utiliser la méthode d'injection par le bas pour verser et augmenter les trous d'aération.
Sable collant
Nom et caractéristiques
Il y a une couche de sable collante près du canal ou à l'intérieur de la pièce moulée, et il y a des bavures ou des creux en relief après le soufflage du sable.
Causes
1. La teneur en impuretés de la poudre réfractaire utilisée dans la couche superficielle du revêtement est trop élevée et ces impuretés réagissent avec le métal fondu pour former un eutectique à bas point de fusion.
2. La température de coulée est trop élevée, en particulier pour les nuances d'acier contenant de l'Al, du Ti et d'autres éléments, ce qui provoque une réaction chimique entre le métal en fusion et la silice.
3. Le réglage du système de déclenchement est déraisonnable et une grande quantité de métal en fusion s'écoule à travers le canal intérieur, provoquant une surchauffe locale.
Méthodes de prévention
1. Utilisez du sable de jade ou de zircon en acier fondu au lieu du sable de silice et essayez de ne pas utiliser de verre soluble comme liant.
2. Réduisez de manière appropriée la température de coulée.
3. Ajoutez un coureur intérieur pour ajuster l'équilibre thermique et réduire la surchauffe locale.
Dilatant
Nom et caractéristiques
Gonflement local sur le plus grand plan de la pièce coulée, ce phénomène est plus évident lorsqu'on utilise du verre soluble comme liant.
Causes
1. La structure de moulage n'est pas raisonnable et la surface plane est trop grande.
2. La coque a une faible résistance à haute température et ne peut pas résister à la pression du métal en fusion.
Méthodes de prévention
1. Améliorez la structure, ajoutez des nervures de traitement ou des trous de traitement sur le plan.
2. Lors de la fabrication de la coque, utilisez des matériaux de coque contenant moins d'impuretés et un caractère réfractaire élevé, ou augmentez l'épaisseur de la coque.
Scories
Nom et caractéristiques
Il y a des scories ou d’autres débris à l’intérieur ou à la surface de la pièce moulée. Les inclusions internes doivent être détectées par inspection aux rayons X ou magnétique.
Causes
1. Les scories sont trop fines et ne sont pas nettoyées avant le taraudage.
2. Les débris sur l'auge de coulée du creuset n'ont pas été nettoyés avant le perçage et ont été introduits dans le métal en fusion.
3. Lors de la coulée, la rétention des scories n'est pas bonne et les scories pénètrent dans la cavité avec le métal en fusion.
Méthodes de prévention
1. Ajustez la composition du laitier avant de le tarauder pour augmenter la viscosité du laitier et faciliter son élimination.
2. Nettoyez les débris dans le bac avant de l'acier pour éviter d'introduire des impuretés dans le métal en fusion dans la poche.
3. Avant la coulée, le fonduacier moulédoit être correctement sédatif pour faciliter la flottaison des scories.
4. Prenez une louche à théière avec un bouchon à laitier ou un filtre en céramique.
Décarburation
Nom et caractéristiques
La teneur en carbone de la couche superficielle de la pièce moulée est inférieure à celle de la matrice.
Causes
1. Pendant la coulée, la température du métal fondu et du moule est élevée et le taux de solidification de la coulée est lent.
2. La profondeur de la couche de décarburation est liée à l'atmosphère de l'environnement de refroidissement de la pièce moulée. Plus la concentration de l'atmosphère oxydante est élevée, plus la décarburation est grave.
Méthodes de prévention
1. Réduisez de manière appropriée la température de coulée et la température du moule pour accélérer la vitesse de refroidissement.
2. Créez artificiellement une atmosphère réductrice autour du moule, par exemple en ajoutant du carbonate de baryum et de la poudre de charbon de bois au moule.
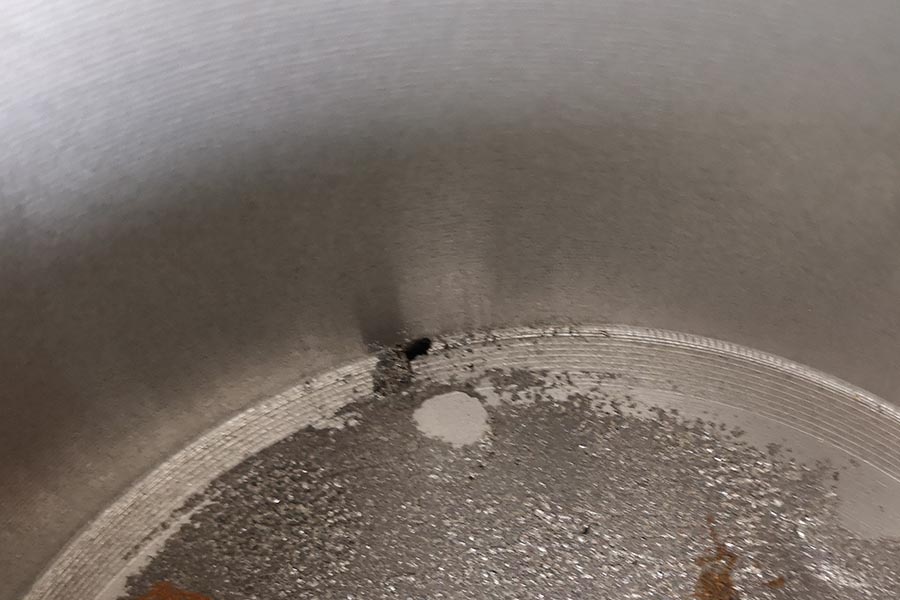
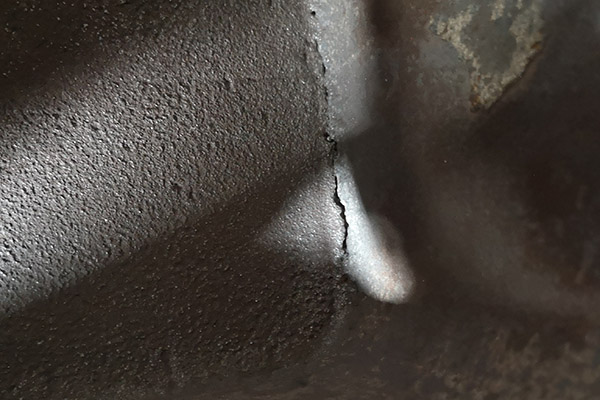
Heure de publication : 22 janvier 2021