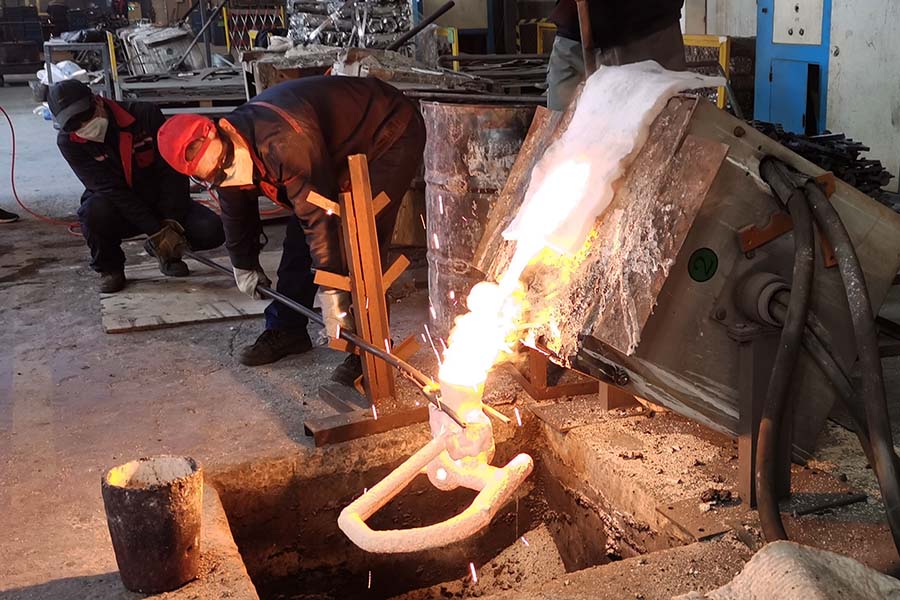
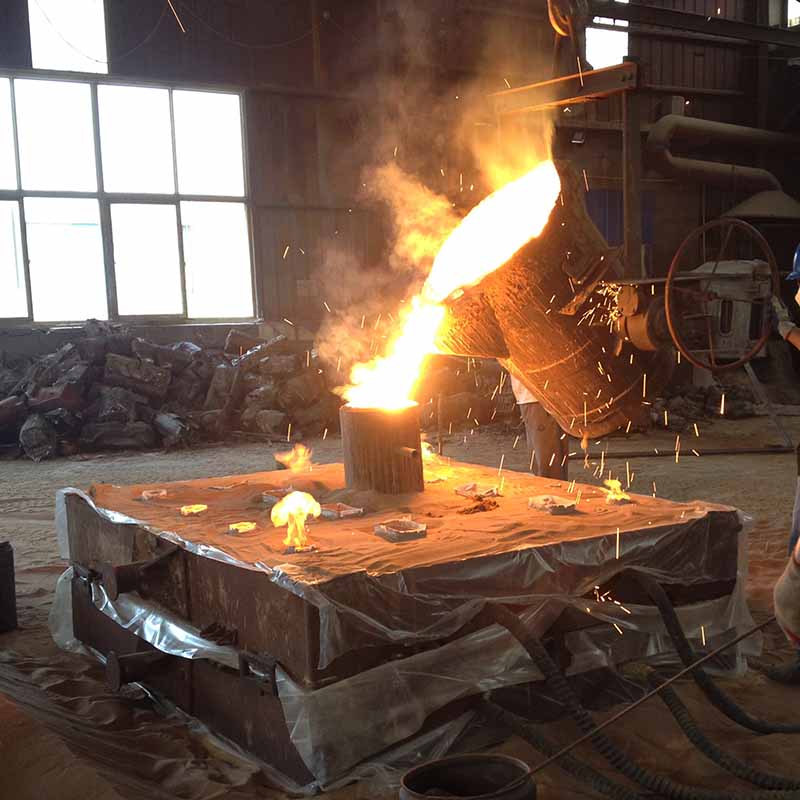
La coulée est l’une des premières méthodes de mise en forme du métal connues de l’être humain. Il s'agit généralement de verser du métal en fusion dans un moule réfractaire comportant une cavité de la forme à réaliser, et de le laisser se solidifier. Quandsolidifié, l'objet métallique désiré est retiré du moule réfractaire soit en cassant le moule, soit en démontant le moule. L'objet solidifié est appelé coulée. Ce processus est également appelé fondage, et l'usine moderne qui se concentre sur la coulée de pièces métalliques est appeléefonderie.
1. Historique du processus de casting
Le processus de coulée a probablement été découvert vers 3500 avant JC en Mésopotamie. Dans de nombreuses régions du monde à cette époque, les haches en cuivre et autres objets plats étaient fabriqués dans des moules ouverts en pierre ou cuits au four.argile. Ces moules étaient essentiellement en une seule pièce. Mais plus tard, lorsqu'il fallait fabriquer des objets ronds, ces moules étaient divisés en deux ou plusieurs parties pour faciliter le retrait des objets ronds.L'âge du bronze (environ 2000 avant JC) a apporté beaucoup plus de raffinement au processus de moulage. Pour la première fois peut-être, on inventait un noyau permettant de réaliser des poches creuses dans les objets. Ces noyaux étaient en terre cuite.En outre, le procédé de cire perdue ou cire perdue était largement utilisé pour la fabrication d'ornements et de travaux fins.
La technologie de moulage a été considérablement améliorée par les Chinois à partir d'environ 1500 avant JC. Avant cela, il n’existe aucune preuve d’une quelconque activité de casting en Chine. Ils ne semblent pas avoir été géniauxJe suis familier avec le procédé de cire perdue et je ne l'utilise pas beaucoup, mais je me spécialise dans les moules multi-pièces pour réaliser des travaux très complexes. Ils ont passé beaucoup de temps à perfectionner le moule dans les moindres détails, de sorte qu'à peinedes travaux de finition étaient nécessaires sur la pièce moulée réalisée à partir des moules. Ils fabriquaient probablement des moules à pièces contenant des pièces soigneusement ajustées, au nombre d'une trentaine ou plus. En fait, de nombreuses moisissures de ce type ont été découvertesurant des fouilles archéologiques dans diverses régions de Chine.
La civilisation de la vallée de l'Indus est également connue pour son utilisation intensive du moulage du cuivre et du bronze pour les ornements, les armes, les outils et les ustensiles. Mais il n’y a pas eu beaucoup d’améliorations technologiques. De la variétéous les objets et figurines exhumés des sites de la vallée de l'Indus, ils semblent avoir été familiers avec toutes les méthodes de coulée connues telles que le moule ouvert, le moule à pièces et le procédé de cire perdue.
Bien que l’on puisse attribuer à l’Inde l’invention de l’acier pour creuset, peu de choses sur la base du fer étaient évidentes en Inde. Il existe des preuves que la production de fer a commencé vers 1000 avant JC en Syrie et en Perse. Il semblequefonte de ferla technologie en Inde est utilisée depuis l’époque de l’invasion d’Alexandre le Grand, vers 300 avant JC.
Le célèbre pilier de fer actuellement situé près du minaret de Qutb à Delhi est un exemple du savoir-faire métallurgique des anciens Indiens. Il mesure 7,2 m de long et est constitué de fonte malléable pure. Ceci est supposé être dupériode de Chandragupta II (375-413 après JC) de la dynastie Gupta. Le taux de rouille de ce pilier, situé à l'extérieur et à l'air libre, est pratiquement nul et même la partie enterrée rouille à un rythme extrêmement lent. Cedoit avoir été d'abord coulé puis martelé jusqu'à la forme finale.
2. Avantages et limites
Le procédé de coulée est largement utilisé dans la fabrication en raison de ses nombreux avantages. Le matériau fondu s'écoule dans n'importe quelle petite section de la cavité du moule et, en tant que tel, dans toute forme complexe - interneou externe – peut être réalisé avec le processus de coulée. Il est possible de couler pratiquement n’importe quel matériau, qu’il soit ferreux ou non ferreux. De plus, les outils nécessaires pour couler les moules sont très simples etpeu coûteux. De ce fait, pour une production d’essai ou une production d’un petit lot, c’est une méthode idéale. Il est possible, lors du processus de coulée, de placer la quantité de matériau là où elle est exactement nécessaire. Par conséquentune réduction de poids dans la conception peut être obtenue.Moulagessont généralement refroidis uniformément de tous les côtés et ne devraient donc avoir aucune propriété directionnelle. Il existe certains métaux et alliagesqui ne peut être traité que par coulée et non par tout autre procédé comme le forgeage en raison de considérations métallurgiques. Des pièces moulées de n'importe quelle taille et poids, même jusqu'à 200 tonnes, peuvent être réalisées.
Cependant, la précision dimensionnelle et la finition de surface obtenues par des méthodes normalesprocédé de moulage au sablene serait pas suffisant pour une application finale dans de nombreux cas. Pour prendre en compte ces cas, quelques castings spéciauxdes procédés tels que le moulage sous pression ont été développés, dont les détails sont donnés dans les chapitres suivants. En outre, le processus de moulage au sable demande dans une certaine mesure beaucoup de main-d'œuvre et de nombreuses améliorations y sont donc destinées.tels que le moulage à la machine et la mécanisation des fonderies. Avec certains matériaux, il est souvent difficile d'éliminer les défauts dus à l'humidité présente dansmoulages en sable.
3. Conditions de diffusion
Dans les chapitres suivants, nous verrons les détails du moulage au sable, qui représente le processus de base du moulage. Avant d'entrer dans les détails du processus, il serait utile de définir un certain nombre de mots de vocabulaire de casting.approprié.
Ballon– Un flacon de moulage est celui qui maintient le moule en sable intact. En fonction de la position du flacon dans la structure du moule, il est désigné par différents noms tels que traînée, chape et joue. Il est composé de boispour des applications temporaires ou plus généralement en métal pour une utilisation de longue durée.
Traîner– Flacon de moulage inférieur
Faire face– Flacon de moulage supérieur
Joue– Flacon de moulage intermédiaire utilisé dans le moulage en trois pièces.
Modèle– Le motif est une réplique de l’objet final à réaliser avec quelques modifications. La cavité du moule est réalisée à l'aide du modèle.
Ligne de séparation– C’est la ligne de démarcation entre les deux flacons de moulage qui composent le moule en sable. Dans le modèle divisé, c'est également la ligne de démarcation entre les deux moitiés du motif.
Conseil inférieur– Il s’agit d’une planche normalement en bois, qui est utilisée au début de la fabrication du moule. Le motif est d'abord conservé sur la planche inférieure, du sable est saupoudré dessus puis le pilonnage est effectué en traînée.
Face au sable– La petite quantité de matière carbonée saupoudrée sur la surface intérieure de la cavité de moulage pour donner une meilleure finition de surface aux pièces moulées
Sable de moulage– Il s’agit du matériau réfractaire fraîchement préparé utilisé pour réaliser la cavité du moule. C'est un mélange d'argile siliceuse et d'humidité dans des proportions appropriées pour obtenir les résultats souhaités et il entoure lemotif lors de la fabrication du moule.
Sable de support– C’est ce qui constitue la majeure partie du matériau réfractaire présent dans le moule. Celui-ci est constitué de sable utilisé et brûlé.
Cœur– Il est utilisé pour réaliser des cavités creuses dans les pièces moulées.
Bassin Verseur– Une petite cavité en forme d’entonnoir au sommet du moule dans laquelle est coulé le métal en fusion.
Éperon– Le passage par lequel le métal en fusion provenant du bassin de coulée atteint la cavité du moule. Dans de nombreux cas, il contrôle le flux de métal dans le moule.
Coureur– Les passages dans le plan de joint à travers lesquels le flux de métal en fusion est régulé avant qu'il n'atteigne la cavité du moule.
Grille– Le point d'entrée réel par lequel le métal en fusion pénètre dans la cavité du moule.
Chapelet– Les chapelets sont utilisés pour soutenir les noyaux à l’intérieur de la cavité du moule afin de supporter leur propre poids et de vaincre les forces métallostatiques.
Froideur– Les refroidisseurs sont des objets métalliques qui sont placés dans le moule pour augmenter la vitesse de refroidissement des pièces moulées afin de fournir une vitesse de refroidissement uniforme ou souhaitée.
Contremarche– Il s’agit d’un réservoir de métal en fusion prévu dans la pièce moulée afin que le métal chaud puisse refluer dans la cavité du moule en cas de réduction de volume de métal due à la solidification.
4. Procédure de fabrication de moules en sable
La procédure de fabrication d’un moule en sable typique est décrite dans les étapes suivantes :
Tout d’abord, une planche inférieure est placée soit sur la plate-forme de moulage, soit sur le sol, pour uniformiser la surface. Le flacon de moulage par traînée est maintenu à l'envers sur la planche inférieure avec la partie traînée dumotif au centre du flacon sur le tableau. Il doit y avoir un jeu suffisant entre le motif et les parois du flacon qui doit être de l'ordre de 50 à 100 mm. Du sable sec est saupoudré surle carton et le motif pour fournir une couche non collante. Du sable de moulage fraîchement préparé et de qualité requise est ensuite versé dans le traîneau et sur le motif sur une épaisseur de 30 à 50 mm. Le reste du flacon de traînée estcomplètement rempli de sable de réserve et uniformément battu pour compacter le sable. Le pilonnage du sable doit être effectué correctement afin de ne pas le compacter trop fort, ce qui rendrait difficile l'échappement des gaz,ni trop lâche, de sorte que le moule n'aurait pas assez de résistance. Une fois le pilonnage terminé, l'excédent de sable présent dans le ballon est entièrement gratté à l'aide d'une barre plate jusqu'au niveau des bords du ballon.
Désormais, avec un fil d'évent, qui est un fil de 1 à 2 mm de diamètre avec une extrémité pointue, des trous d'évent sont pratiqués dans la traînée sur toute la profondeur du ballon ainsi que dans le motif pour faciliter l'évacuation des gaz. pendant le castingsolidification. Ceci termine la préparation de la traînée.
Le flacon de traînée fini est maintenant roulé sur la planche inférieure, exposant le motif comme indiqué sur la photo. À l'aide d'une nappe, les bords du sable autour du motif sont réparés et la moitié du motif est placée dessus.le motif de traînée, en l'alignant à l'aide de goujons. Le flacon de copeau au-dessus de la traînée est situé à nouveau en s'alignant à l'aide des épingles. Le sable de séparation sec est saupoudré sur toute la traînée et sur le motif.
Une tige d'injection permettant de réaliser le passage de la carotte est située à une petite distance d'environ 50 mm du motif. De plus, la goupille de montée, si nécessaire, est conservée à un endroit approprié et du sable de moulage fraîchement préparé similaire à celui-ci.de la traînée avec le sable de support est saupoudré. Le sable est soigneusement damé, l'excédent de sable est gratté et des trous d'aération sont pratiqués partout dans la chape comme dans la traînée.
La tige de coulée et la tige de colonne montante sont soigneusement retirées du flacon. Plus tard, le bassin de coulée est découpé près du sommet de la carotte. La chape est séparée de la traînée et de tout sable meuble sur l'interface chape et traînée.de la traînée est évacuée à l'aide d'un soufflet. Maintenant, la chape et les moitiés du motif de traînée sont retirées en utilisant les pointes de tirage et en frappant le motif tout autour pour agrandir légèrement la cavité du moule afin que leles parois du moule ne sont pas gâchées par le motif de retrait. Les coulisses et les portails sont découpés dans le moule avec soin sans abîmer le moule. Tout excès ou sable meuble trouvé dans les glissières et la cavité du moule est souffléà l'aide du soufflet. Désormais, le sable de parement sous forme de pâte est appliqué sur toute la cavité du moule et sur les canaux, ce qui confère à la pièce moulée finie une bonne finition de surface.
Un noyau de sable sec est préparé à l'aide d'une boîte à noyaux. Après une cuisson adaptée, il est placé dans la cavité du moule comme indiqué sur la photo. La chape est replacée sur la traînée en prenant soin de l'alignement des deux au moyen duépingles. Un poids approprié est maintenu sur la chape pour prendre en charge la force métallostatique ascendante pendant la coulée du métal en fusion. Le moule, comme le montre la photo, est maintenant prêt à être coulé.
Heure de publication : 25 décembre 2020